What are Cable Cleats? The Definitive Guide
What are cable cleats?
Cable cleats (also known as cable clamps) are an essential component when installing cable and recommended in every electrical installation. This article aims to answer FAQ on Cable Clamps and Cleats, like: what are cable cleats, when to use cable cleats, cable cleat types & specification, correct cleat spacing, how to fix cable cleats and more.
According to IEC 61914:2009, Cable Cleats are “devices designed to provide securing of cables when installed at intervals along the length of the cables”. In other words, they are devices that ensure the retention and support of cables, restrict the cable movement and provide resistance to electro-mechanical forces.
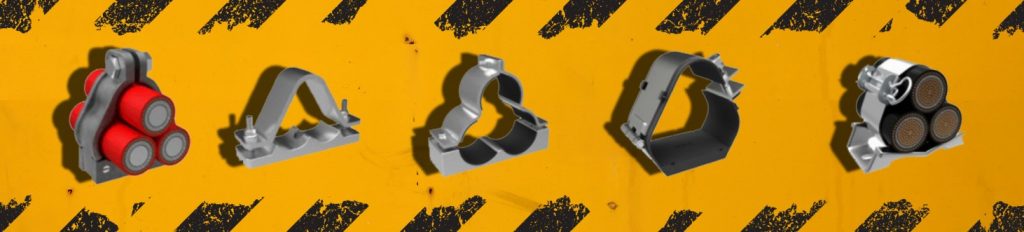
Why use cable cleats? When are cable cleats required?
A cable cleat is designed to ensure that cables are fixed, retained and supported correctly so that in the event of short circuit fault or any other emergency, they will contain the cables without causing damage; enabling the circuit to be restored once the fault has been dealt with.
Failure to correctly clamp the cable could result in a break in the flow of electricity and have serious consequences. Apart from the aforementioned, their importance also lies in:
- Supporting cables and conductors & preventing excessive cable movement, making reworking easier and safer.
- Providing restraint and protecting against the effects of electro-dynamic forces, developing during a short circuit or earth fault.
- Reducing the mechanical load the cable may be exposed to under its own weight and the load the cable termination may be exposed to.
- Facilitating a neat and orderly installation, allowing use of cables at their optimum ratings, whilst maximising the use of the available space.
- Attaching the cables to a mounting surface (ladder, tray, strut, or rail, wire and beam), without relying though on the mounting surface for the retention of the cables.
Despite the importance of cable cleats, there were no British or International standards for them for many years. Prysmian Components, leading cable cleat manufacturer, actively participated in and supported the creation of the European Standard and its progress to becoming the current International Standard (BS EN 61914:2009 – IEC 61914). IEC 61914 manifested the importance of cable cleat products and correct cable cleat fixing/ spacing. Most importantly, it highlighted the significance of the protection of cable management systems and the potential risks to human life in applications where there is no use of cable cleats.
Types of Cable Cleats
When it comes to cable cleats, two main types stand out: metal and plastic, each with unique advantages and applications.
Metal cable cleats, like the Prysmian Single Way Claw Cleat (370BA), manufactured from aluminium alloy, excel in securing single cables. Options range from non-conductive aluminum to stainless steel, with innovative choices like the Prysmian Sirius Trefoil Cleat (379TC) featuring an LSOH (low smoke, zero halogen) lining.
Plastic cable cleats, exemplified by the Prysmian Single Way Telcleat (385AA), offer versatility for various cable diameters. Their UV and weather-resistant fixing point allows for double stacking, securing two cables on a single fixing. With wide operating temperature ranges and exceptional durability, plastic cable cleats present an affordable and reliable solution for demanding environments.
Selecting the perfect Cleat
“-Which cable cleating should I use?”
“-What size cable cleat for…”
Those are some of the most common questions our Sales team listens to when it comes to cable cleat/ clamp specification. And the answer is always the same, “it depends”!
E-Tech Components can offer huge ranges of single, trefoil, quad cleats and bespoke solutions. All of the above designed and manufactured according to the application’s requirements from leading industry cleat manufacturers.
Cable Cleat Specification
To specify the perfect cleat for your application, we take into consideration a big list of factors:
- Cable Formation: The Cable Formation/ Configuration of the system (Parallel/ Flat Formation of Single Core Cables, Trefoil Formation, Multicore Cable) will define the type of cable cleat required. That could be a Single, Trefoil, Quad Cleat, or this may even indicate that a bespoke solution may be necessary.
- Cable Type: One of the main factors during cable cleat specification is the type of cable, Single or Multi-core. Another one is its Voltage Level and Construction {Low Voltage (LV), Medium Voltage (MV) or High Voltage (HV)}.
- Cable Diameter: Overall Diameter of the LV or HV Cable will allow us to choose the correct size cleat. This dimension, the Outside Cable Diameter around the cable sheath, is also one of the requirements for calculating the short circuit forces the cable clamp may be subject to under fault conditions.
- Performance: Depending on the electrical installation application, the cleat might have to include material performance and cable cleat specification features to adhere to such as Fire Resistance (FR), Low Smoke Zero Halogen (LS0H/ LSZH), Low Smoke & Fume (LSF), Corrosion Resistance (Stainless Steel) and more.
- Short Circuit Rating – Maximum Peak Fault (kA): The Maximum Peak Fault the cable may be subject to, under short circuit conditions.
- Expansion & Contraction: Some cables expand and contract more than others due to changes in temperature. When constraining the cable, considerable forces can be transferred to the supporting structure. To tackle this, single core cables are generally “snaked” making slight loops to take up the expansion and contraction.
Other factors include power system design, mechanical load, cable management structure and installation environment.
How to fix/ install cable cleats?
However, selecting the correct cable cleat (specification), is only part of the job. The power cable system designer or installer has an obligation to consider the method of fixing and installing cables to cleats, in order to restrain cable movement whether caused by an electrical fault or any other reason. As a rule of thumb, cleats should be firmly fixed, using supports of strength adequate to withstand forces corresponding to the values of the peak prospective short-circuit current.
Generally, cable cleats are fastened around cables by a threaded bolt and nut. The higher the torque when closing this fixing, the tighter the grip of the cleat to the cable. Having a tight grip of the cleat around the cable can be advantageous when it comes to axial slippage, BUT over-tightening can lead to damage to both the outer sheath jacket and the construction of the cable.
Recommendation: Cleat fixings should be tightened up until the cleat is fastened around the cable tight enough to not leave any gaps between the liner of the cleat and the cable, and with no visible damage or bulging to the outer jacket.
Correct Cleat Spacing
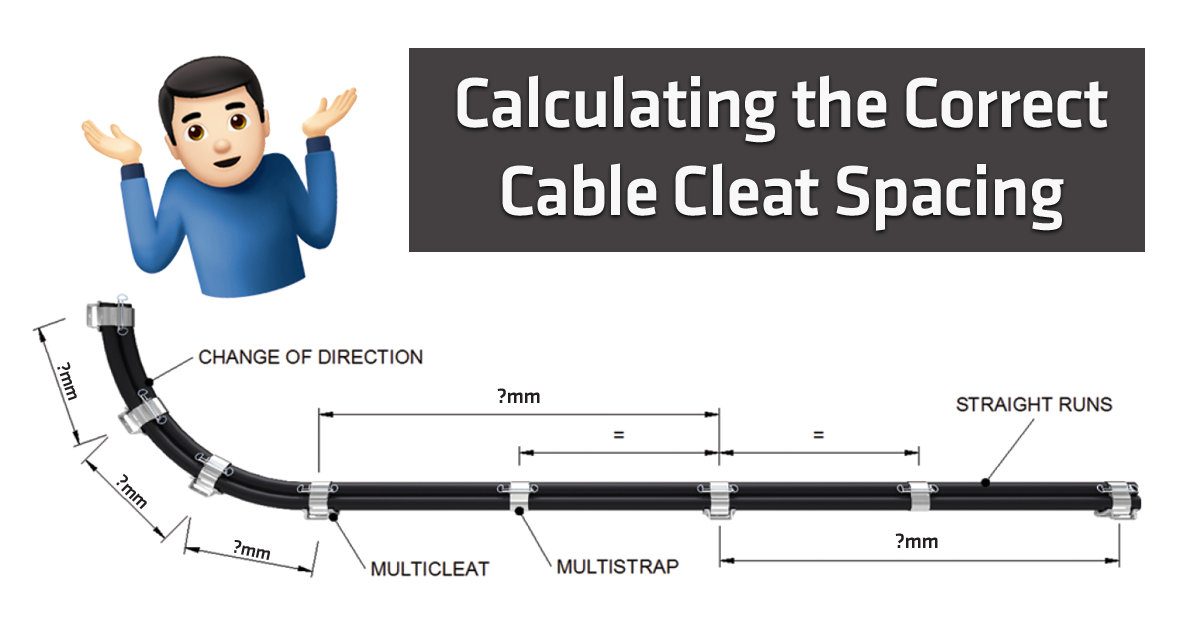
Single Cables
Correct Cable Cleat Spacing in accessible positions:
MAXIMUM SPACING OF CABLE FIXINGS | ||||||
Overall Diameter of cable² (OD) | Non-armoured thermosetting, thermoplastic or lead sheathed cables and non-armoured fire resisting cables | Single-wire armoured cables including fire resisting armoured cable | Mineral insulated copper sheathed or Aluminium sheathed cables | |||
Horizontal5 2 | Vertical5 3 | Horizontal5 6 | Vertical5 7 | Horizontal5 8 | Vertical5 9 | |
OD ≤ 9 mm | 250 mm | 400 mm | – | – | 600 mm | 800 mm |
9 mm < OD ≤ 15 mm | 300 mm | 400 mm | 350 mm | 450 mm | 900 mm | 1200 mm |
15 mm < OD ≤ 20 mm | 350 mm | 450 mm | 400 mm | 550 mm | 1500 mm | 2000 mm |
20 mm < OD ≤ 40 mm | 400 mm | 550 mm | 450 mm | 600 mm | – | – |
40 mm < OD ≤ 50 mm | 600 mm | 800 mm | 900 mm | 1100 mm | – | – |
50 mm < OD ≤ 60 mm | 750 mm | 1000 mm | 950 mm | 1100 mm | – | – |
60 mm < OD ≤ 70 mm | 900 mm | 1200 mm | 1000 mm | 1200 mm | – | – |
OD ≥ 70 mm | 1000 mm | 1400 mm | 1200 mm | 1400 mm | – | – |
Notes:
- Installer should use fire resistant fixings for fire resistant cables.
- For flat cables taken as the dimension of the major axis.
- The spacings shown above apply to multi-core cables.
- The spacing of fixings on single core cables in a.c. installations must take account of the magnitude of forces generated under fault conditions.
- You can use the spacings stated for horizontal runs to runs angled at more than 30° from the vertical.
- For runs at an angle of 30° or less from the vertical, spacing suggestions are applicable.
Trefoil Cables
When a short circuit fault occurs in a three-phase system, there is a period of extreme asymmetry, followed by a steadier more symmetric state.
The degree of asymmetry depends on when in the cycle the fault initiation takes place, butalso the nature of the fault (e.g. 3–phase to earth). By convention, the “Peak” is the maximum current value in the early asymmetrical period and it is at this point that the highest instantaneous force between the cables occurs.
Where the system peak fault current and the cable diameter are available, BS EN 61914:2009 (IEC 61914) provides a formula which enables us to calculate the maximum force on a cable conductor.
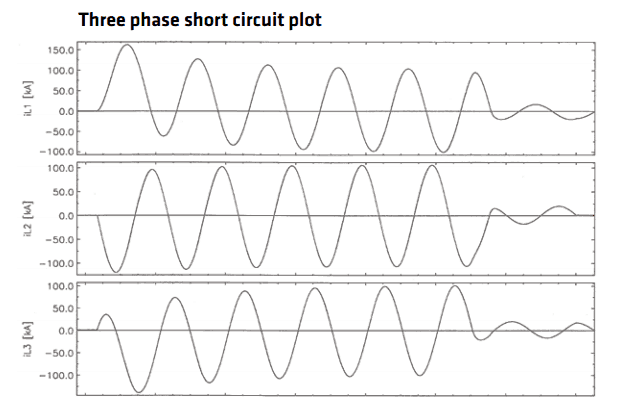
Ft= 0.17 x ip2 / S (B.4)
Where:
Ft is the maximum force on the cable conductor in a trefoil configuration for a three phase short circuit [N/m]
ip is the peak short-circuit current [kA]
S is the centre to centre distance between two neighbouring conductors [m] (for Trefoil arrangements S=Cable Diameter)
Short circuit tests in accordance with BS EN 61914:2009 take place on the most critical cleat size within its range. The Formula’s (B.4) use can then calculate the maximum F during the test. This maximum force figure can then be used when specifying alternative configurations of the cable size and fault current. Calculate the theoretical Ft for the alternative configuration and ensure it is smaller or equal to the tested value.
Trefoil Cable Cleat Spacing
Trefoil Cleats that are required to withstand the high forces generated by high short circuit currents will often be spaced at very regular intervals – typically matching the commonly available cable ladder (i.e. 300 mm / 225 mm).
The maximum short circuit current values will be quoted with the test information for each design of trefoil cleats. If a system uses larger cables or has a lower fault current it may be possible to broaden these spacings. (Contact our Technical Team for help)
Generally, to create and maintain a satisfactory trefoil installation, leave a maximum strap/ cable cleat spacing of 900 mm.cable cleats for electrical
E-Tech Components – Cable Management & Cleats
E-Tech Components offer a huge range of different types Cable Cleats & Clamps, from Single Way and Trefoil ,to Quad Cleats and Bespoke Solutions designed and manufactured according to your application’s requirements.
We work with the largest global cable manufacturer, The Prysmian Group, and distribute to major projects throughout the world. Prysmian’s BICON range of cable cleats and clamps are tried, tested and certified to the latest international standards. We also work with Slagboom Electric and their range of Dutchclamp Non Metallic Single Way and Trefoil Cleats.
Our portfolio is massive, so don’t hesitate to contact our Technical Sales Team to help you choose the perfect cleat.
FREE Technical Advisory Service
E-Tech Components UK Ltd maintains a free technical advisory service.
Contact us about any questions, enquiries or requests you may have: +44 (0) 1744 762 929